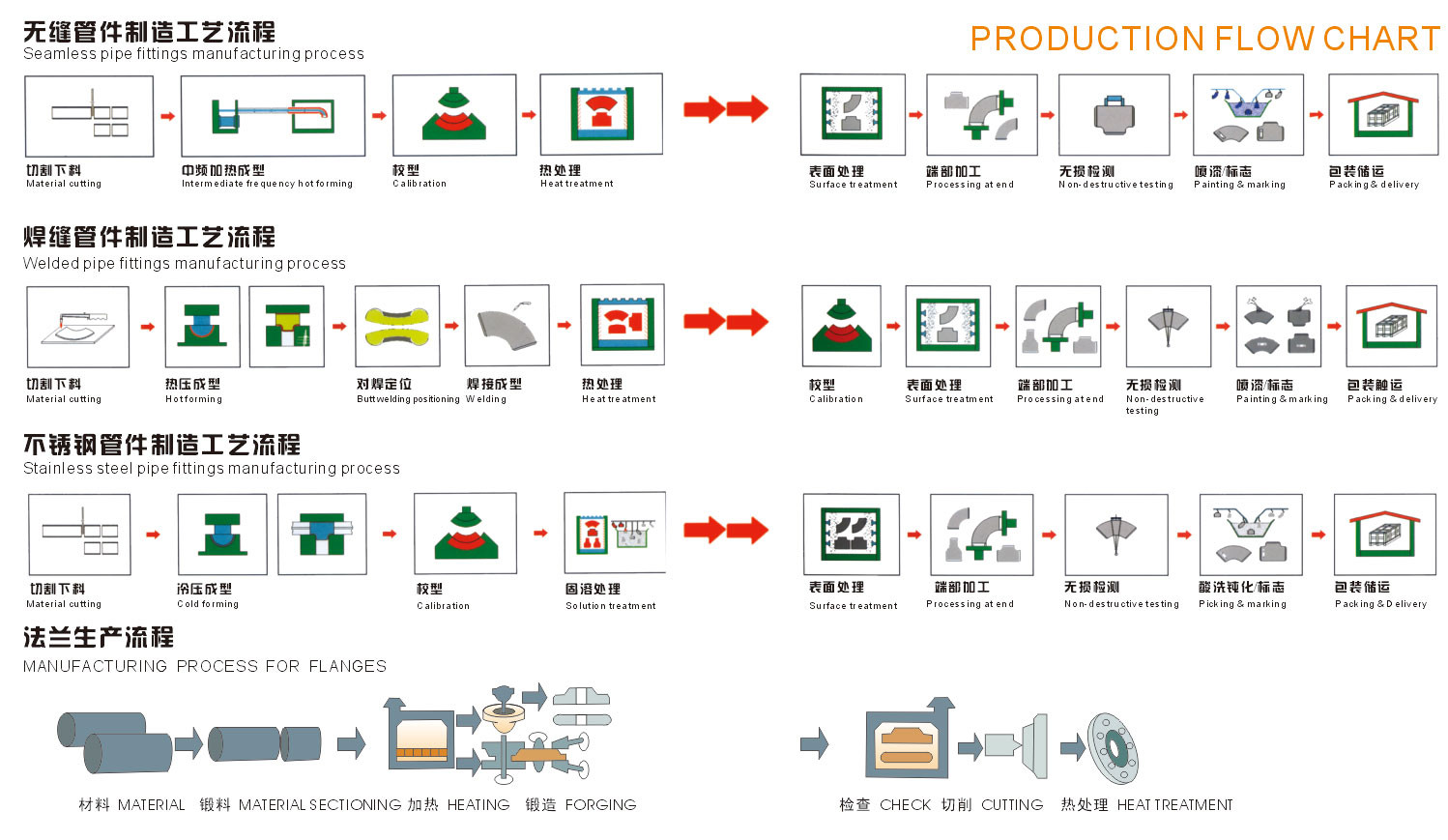
1. วัสดุ
1.1.การเลือกวัสดุต้องเป็นไปตามมาตรฐานที่เกี่ยวข้องของประเทศผู้ผลิตท่อและมาตรฐานวัตถุดิบที่เจ้าของกำหนด
1.2.หลังจากเข้าไปในโรงงานแล้ว ผู้ตรวจสอบจะตรวจสอบใบรับรองวัสดุเดิมที่ออกโดยผู้ผลิตและรายงานการตรวจสอบสินค้าโภคภัณฑ์ของผู้นำเข้าก่อนตรวจสอบว่าเครื่องหมายบนวัสดุมีความสมบูรณ์และสอดคล้องกับใบรับรองคุณภาพหรือไม่
1.3.ตรวจสอบวัสดุที่ซื้อใหม่ ตรวจสอบองค์ประกอบทางเคมี ความยาว ความหนาของผนัง เส้นผ่านศูนย์กลางภายนอก (เส้นผ่านศูนย์กลางภายใน) และคุณภาพพื้นผิวของวัสดุอย่างเคร่งครัดตามข้อกำหนดมาตรฐาน และบันทึกหมายเลขชุดงานและหมายเลขท่อของวัสดุไม่อนุญาตให้จัดเก็บและแปรรูปวัสดุที่ไม่เหมาะสมพื้นผิวภายในและภายนอกของท่อเหล็กต้องไม่มีรอยแตก รอยพับ รอยพับ ตกสะเก็ด หลุดลอก และเส้นขนข้อบกพร่องเหล่านี้จะถูกลบออกอย่างสมบูรณ์ความลึกในการขจัดจะต้องไม่เกินค่าเบี่ยงเบนเชิงลบของความหนาของผนังที่ระบุ และความหนาของผนังจริงที่สถานที่ทำความสะอาดต้องไม่น้อยกว่าความหนาของผนังขั้นต่ำที่อนุญาตบนพื้นผิวด้านในและด้านนอกของท่อเหล็ก ขนาดข้อบกพร่องที่อนุญาตจะต้องไม่เกินข้อกำหนดที่เกี่ยวข้องในมาตรฐานที่สอดคล้องกัน มิฉะนั้น จะถูกปฏิเสธมาตราส่วนออกไซด์บนพื้นผิวด้านในและด้านนอกของท่อเหล็กจะต้องถูกลบออกและบำบัดด้วยการป้องกันการกัดกร่อนการรักษาป้องกันการกัดกร่อนจะไม่ส่งผลต่อการตรวจสอบด้วยสายตาและสามารถถอดออกได้
1.4.คุณสมบัติทางกล
คุณสมบัติทางกลต้องเป็นไปตามมาตรฐานตามลำดับ และองค์ประกอบทางเคมี มิติทางเรขาคณิต ลักษณะที่ปรากฏ และคุณสมบัติทางกลต้องได้รับการตรวจสอบและยอมรับอีกครั้ง
1.5 ประสิทธิภาพของกระบวนการ
1.5.1.ท่อเหล็กจะต้องได้รับการทดสอบแบบไม่ทำลายด้วยอัลตราโซนิก 100% ทีละรายการตาม SEP1915 และต้องมีตัวอย่างมาตรฐานสำหรับการทดสอบอัลตราโซนิกความลึกของข้อบกพร่องของตัวอย่างมาตรฐานจะต้องเป็น 5% ของความหนาของผนัง และสูงสุดต้องไม่เกิน 1.5 มม.
1.5.2.ท่อเหล็กจะต้องได้รับการทดสอบการแบน
1.5.3.ขนาดเกรนจริง
ขนาดเกรนจริงของท่อสำเร็จรูปต้องไม่หนากว่าเกรด 4 และความแตกต่างของเกรดของท่อเหล็กที่มีเลขความร้อนเท่ากันจะต้องไม่เกินเกรด 2 ขนาดเกรนต้องได้รับการตรวจสอบตามมาตรฐาน ASTM E112
2. การตัดและการทำให้ว่างเปล่า
2.1.ก่อนทำการตัดช่องว่างของข้อต่อท่อโลหะผสม จะต้องดำเนินการคำนวณวัสดุที่ถูกต้องก่อนจากผลการคำนวณความแข็งแรงของข้อต่อท่อ ให้วิเคราะห์และพิจารณาอิทธิพลของปัจจัยหลายๆ อย่าง เช่น การบางและการเสียรูปของข้อต่อท่อในกระบวนการผลิตต่อส่วนสำคัญของข้อต่อท่อ (เช่น ส่วนโค้งด้านนอกของข้อศอก ความหนาของแท่นที ไหล่ ฯลฯ ) และเลือกวัสดุที่มีค่าเผื่อเพียงพอ และพิจารณาว่าค่าสัมประสิทธิ์การเสริมแรงหลังการขึ้นรูปข้อต่อท่อสอดคล้องกับค่าสัมประสิทธิ์ความเค้นที่ออกแบบของท่อและพื้นที่การไหลของท่อหรือไม่การชดเชยวัสดุแนวรัศมีและการชดเชยวัสดุไหล่ระหว่างกระบวนการกดจะต้องคำนวณสำหรับแท่นกดร้อน
2.2.สำหรับวัสดุท่อโลหะผสม เครื่องตัดสายพานแบบโครงสำหรับตั้งสิ่งของใช้สำหรับการตัดแบบเย็นสำหรับวัสดุอื่นๆ โดยทั่วไปจะหลีกเลี่ยงการตัดด้วยเปลวไฟ แต่การตัดแบบสายพานจะใช้เพื่อป้องกันข้อบกพร่อง เช่น ชั้นแข็งหรือรอยแตกที่เกิดจากการทำงานที่ไม่เหมาะสม
2.3.ตามข้อกำหนดของการออกแบบ เมื่อตัดและปิดผิว เส้นผ่านศูนย์กลางภายนอก ความหนาของผนัง วัสดุ หมายเลขท่อ หมายเลขแบทช์ของเตาเผา และหมายเลขการไหลของวัตถุดิบสำหรับท่อฟิตติ้งจะถูกทำเครื่องหมายและย้าย และการระบุจะต้องอยู่ในรูปของ ซีลเหล็กความเค้นต่ำและการพ่นสีและบันทึกเนื้อหาการดำเนินการลงในการ์ดขั้นตอนการผลิต
2.4.หลังจากล้างชิ้นแรกแล้ว ผู้ปฏิบัติงานจะต้องดำเนินการตรวจสอบตนเองและรายงานต่อผู้ตรวจพิเศษของศูนย์ทดสอบเพื่อตรวจสอบพิเศษหลังจากผ่านการตรวจสอบแล้ว ให้ทำการตัดช่องว่างของชิ้นส่วนอื่น และจะต้องทดสอบและบันทึกแต่ละชิ้น
3. แม่พิมพ์กดร้อน (ดัน)
3.1.กระบวนการกดร้อนของข้อต่อท่อ (โดยเฉพาะ TEE) เป็นกระบวนการที่สำคัญ เตาให้ความร้อนน้ำมันสามารถให้ความร้อนช่องว่างได้ก่อนให้ความร้อนแก่ตัวเปล่า ก่อนอื่นให้ทำความสะอาดมุมเศษ น้ำมัน สนิม ทองแดง อลูมิเนียม และโลหะจุดหลอมเหลวต่ำอื่นๆ บนพื้นผิวของท่อเปล่าด้วยเครื่องมือ เช่น ค้อนและล้อเจียรตรวจสอบว่ารหัสเปล่าตรงตามข้อกำหนดการออกแบบหรือไม่
3.2.ทำความสะอาดของกระจุกกระจิกในห้องโถงเตาทำความร้อน และตรวจสอบว่าวงจรเตาทำความร้อน วงจรน้ำมัน รถเข็นและระบบวัดอุณหภูมิเป็นปกติหรือไม่ และน้ำมันเพียงพอหรือไม่
3.3.วางช่องว่างในเตาให้ความร้อนเพื่อให้ความร้อนใช้อิฐทนไฟเพื่อแยกชิ้นงานออกจากแท่นเตาหลอมในเตาหลอมควบคุมความเร็วความร้อนอย่างเข้มงวด 150 ℃ / ชั่วโมงตามวัสดุต่างๆเมื่อให้ความร้อนสูงถึง 30-50 ℃เหนือ AC3 ฉนวนจะต้องมากกว่า 1 ชั่วโมงในกระบวนการให้ความร้อนและเก็บรักษาความร้อน ต้องใช้จอแสดงผลดิจิตอลหรือเทอร์โมมิเตอร์อินฟราเรดเพื่อติดตามและปรับเปลี่ยนได้ตลอดเวลา
3.4.เมื่อชิ้นงานถูกทำให้ร้อนถึงอุณหภูมิที่กำหนด จะถูกปล่อยออกจากเตาเผาเพื่อกดการกดเสร็จสิ้นด้วยการกด 2500 ตันและดายรัดท่อในระหว่างการกด อุณหภูมิของชิ้นงานในระหว่างการกดจะถูกวัดด้วยเทอร์โมมิเตอร์อินฟราเรด และอุณหภูมิไม่ต่ำกว่า 850 ℃เมื่อชิ้นงานไม่เป็นไปตามข้อกำหนดในคราวเดียวและอุณหภูมิต่ำเกินไป ชิ้นงานจะถูกส่งไปยังเตาเผาเพื่อให้ความร้อนซ้ำและเก็บรักษาความร้อนก่อนกด
3.5.การขึ้นรูปร้อนของผลิตภัณฑ์พิจารณากฎการไหลของโลหะของการเปลี่ยนรูปเทอร์โมพลาสติกอย่างครบถ้วนในกระบวนการขึ้นรูปของผลิตภัณฑ์สำเร็จรูปแม่พิมพ์ที่ขึ้นรูปแล้วจะพยายามลดความต้านทานการเปลี่ยนรูปที่เกิดจากกระบวนการแปรรูปที่ร้อนของชิ้นงาน และแม่พิมพ์ยางแบบอัดจะอยู่ในสภาพดีแม่พิมพ์ยางได้รับการตรวจสอบอย่างสม่ำเสมอตามข้อกำหนดของระบบประกันคุณภาพ ISO9000 เพื่อควบคุมปริมาณการเสียรูปของเทอร์โมพลาสติกของวัสดุ เพื่อให้ความหนาของผนังจริงของจุดใดๆ บนข้อต่อท่อมากกว่าความหนาของผนังขั้นต่ำ ท่อตรงที่เชื่อมต่อ
3.6.สำหรับข้อศอกที่มีเส้นผ่านศูนย์กลางขนาดใหญ่จะใช้การขึ้นรูปแบบความร้อนความถี่ปานกลางและเลือกเครื่องกดข้อศอกขนาดใหญ่พิเศษ tw1600 เป็นอุปกรณ์ผลักดันในกระบวนการดัน อุณหภูมิความร้อนของชิ้นงานจะถูกปรับโดยการปรับกำลังของแหล่งจ่ายไฟความถี่ปานกลางโดยทั่วไปการกดจะถูกควบคุมที่ 950-1020 ℃ และความเร็วในการผลักจะถูกควบคุมที่ 30-100 มม. / นาที
4. การรักษาความร้อน
4.1.สำหรับอุปกรณ์ท่อสำเร็จรูป บริษัทของเราดำเนินการบำบัดความร้อนอย่างเคร่งครัดตามระบบบำบัดความร้อนที่ระบุไว้ในมาตรฐานที่สอดคล้องกันโดยทั่วไป การอบชุบด้วยความร้อนของข้อต่อท่อขนาดเล็กสามารถทำได้ในเตาหลอมแบบต้านทาน และการรักษาความร้อนของข้อต่อท่อหรือข้อศอกที่มีเส้นผ่านศูนย์กลางขนาดใหญ่สามารถทำได้ในเตาบำบัดความร้อนด้วยน้ำมันเชื้อเพลิง
4.2.ห้องโถงของเตาเผาความร้อนต้องสะอาดและปราศจากน้ำมัน เถ้า สนิมและโลหะอื่น ๆ ที่แตกต่างจากวัสดุบำบัด
4.3.การรักษาความร้อนจะต้องดำเนินการอย่างเคร่งครัดตามเส้นโค้งการรักษาความร้อนที่กำหนดโดย "บัตรกระบวนการบำบัดความร้อน" และอุณหภูมิที่เพิ่มขึ้นและความเร็วในการตกของชิ้นส่วนท่อเหล็กโลหะผสมจะต้องควบคุมให้น้อยกว่า 200 ℃ / ชั่วโมง
4.4.เครื่องบันทึกอัตโนมัติจะบันทึกการขึ้นและลงของอุณหภูมิเมื่อใดก็ได้ และปรับอุณหภูมิและระยะเวลาในเตาหลอมโดยอัตโนมัติตามพารามิเตอร์ที่กำหนดไว้ล่วงหน้าในระหว่างกระบวนการให้ความร้อนของอุปกรณ์ท่อ เปลวไฟจะถูกปิดกั้นด้วยกำแพงกันไฟเพื่อป้องกันไม่ให้เปลวไฟพ่นลงบนพื้นผิวของข้อต่อท่อโดยตรง เพื่อให้แน่ใจว่าอุปกรณ์ท่อจะไม่ร้อนเกินไปและเผาไหม้ในระหว่างการอบชุบด้วยความร้อน
4.5.หลังจากการอบชุบด้วยความร้อน การตรวจทางโลหะวิทยาจะต้องดำเนินการสำหรับอุปกรณ์ท่อโลหะผสมทีละรายการขนาดเกรนจริงต้องไม่หนากว่าเกรด 4 และเกรดความแตกต่างของข้อต่อท่อที่มีเลขความร้อนเท่ากันจะต้องไม่เกินเกรด 2
4.6.ทำการทดสอบความแข็งบนข้อต่อท่อที่ผ่านการอบชุบด้วยความร้อนเพื่อให้แน่ใจว่าค่าความแข็งของส่วนใดส่วนหนึ่งของข้อต่อท่อไม่เกินช่วงที่กำหนดโดยมาตรฐาน
4.7.หลังจากการอบชุบด้วยความร้อนของอุปกรณ์ท่อ มาตราส่วนออกไซด์บนพื้นผิวด้านในและด้านนอกจะถูกลบออกโดยการพ่นทรายจนกว่าวัสดุที่มองเห็นได้จะแวววาวเป็นโลหะรอยขีดข่วน หลุม และข้อบกพร่องอื่น ๆ บนพื้นผิวของวัสดุจะต้องขัดให้เรียบด้วยเครื่องมือเช่นล้อเจียรความหนาของอุปกรณ์ท่อขัดเงาต้องไม่น้อยกว่าความหนาของผนังขั้นต่ำที่กำหนดโดยการออกแบบ
4.8.กรอกบันทึกการรักษาความร้อนตามหมายเลขข้อต่อท่อและการระบุ และเขียนการระบุที่ไม่สมบูรณ์บนพื้นผิวของข้อต่อท่อและโฟลว์การ์ดอีกครั้ง
5. การประมวลผลร่อง
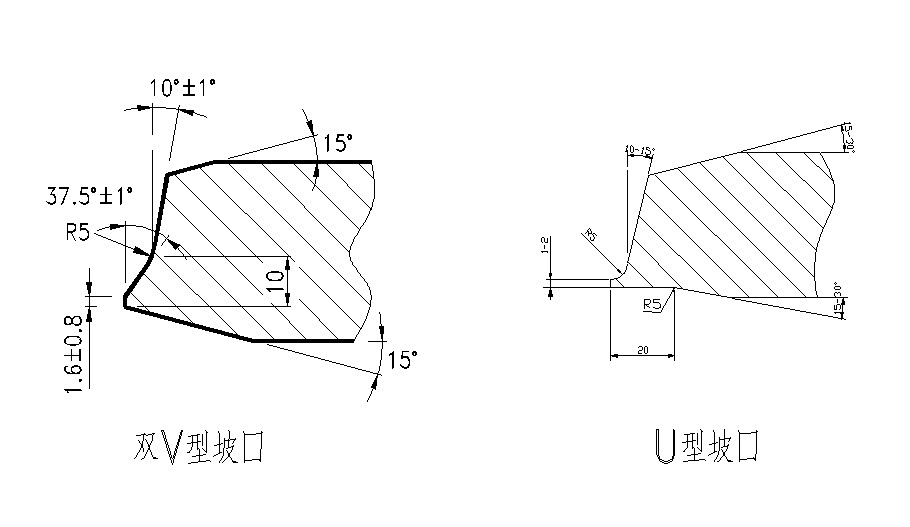
5.1.การประมวลผลร่องของอุปกรณ์ท่อทำได้โดยการตัดด้วยกลไกบริษัทของเรามีอุปกรณ์ตัดเฉือนมากกว่า 20 ชุด เช่น เครื่องกลึงต่างๆ และหัวจ่ายไฟ ซึ่งสามารถแปรรูปร่องรูปตัววีหรือรูปตัวยูคู่ ร่องใน และร่องนอกของข้อต่อท่อผนังหนาต่างๆ ได้ตามความต้องการของลูกค้า .บริษัทสามารถดำเนินการตามแบบร่องและข้อกำหนดทางเทคนิคที่ลูกค้ากำหนด เพื่อให้แน่ใจว่าอุปกรณ์ท่อนั้นใช้งานง่ายและเชื่อมในกระบวนการเชื่อม
5.2.หลังจากร่องติดตั้งท่อเสร็จสมบูรณ์ ผู้ตรวจสอบจะต้องตรวจสอบและยอมรับขนาดโดยรวมของข้อต่อท่อตามข้อกำหนดการวาดภาพ และทำผลิตภัณฑ์ใหม่ด้วยมิติทางเรขาคณิตที่ไม่มีเงื่อนไขจนกว่าผลิตภัณฑ์จะมีขนาดตามการออกแบบ
6. ทดสอบ
6.1.อุปกรณ์ท่อจะต้องได้รับการทดสอบตามข้อกำหนดมาตรฐานก่อนออกจากโรงงานตาม ASME B31.1การทดสอบทั้งหมดจะต้องเสร็จสิ้นโดยผู้ตรวจสอบมืออาชีพที่มีคุณสมบัติที่สอดคล้องกันซึ่งเป็นที่ยอมรับโดยสำนักกำกับดูแลด้านเทคนิคของรัฐ
6.2.การทดสอบอนุภาคแม่เหล็ก (MT) จะต้องดำเนินการบนพื้นผิวด้านนอกของแท่นที ศอกและรีดิวเซอร์ การวัดความหนาอัลตราโซนิกและการตรวจจับข้อบกพร่องจะต้องดำเนินการที่ด้านอาร์คด้านนอกของข้อศอก ไหล่ทีบ่า และส่วนรีดิวเซอร์ และการตรวจจับจุดบกพร่องด้วยรังสี หรือการตรวจจับข้อบกพร่องด้วยคลื่นเสียงความถี่สูงจะต้องดำเนินการบนรอยเชื่อมของอุปกรณ์เชื่อมท่อทีออฟหรือข้อศอกปลอมจะต้องได้รับการทดสอบอัลตราโซนิกบนช่องว่างก่อนการตัดเฉือน
6.3.การตรวจจับข้อบกพร่องของอนุภาคแม่เหล็กจะต้องดำเนินการภายใน 100 มม. จากร่องของอุปกรณ์ท่อทั้งหมดเพื่อให้แน่ใจว่าไม่มีรอยแตกและข้อบกพร่องอื่น ๆ ที่เกิดจากการตัด
6.4.คุณภาพพื้นผิว: พื้นผิวภายในและภายนอกของข้อต่อท่อต้องไม่มีรอยแตก, โพรงหดตัว, เถ้า, ทรายเกาะ, พับ, รอยเชื่อมขาด, ผิวสองชั้น และข้อบกพร่องอื่นๆพื้นผิวต้องเรียบไม่มีรอยแหลมคมความลึกของภาวะซึมเศร้าต้องไม่เกิน 1.5 มม.ขนาดสูงสุดของความหดหู่ใจต้องไม่เกิน 5% ของเส้นรอบวงของท่อและไม่เกิน 40 มม.พื้นผิวเชื่อมต้องไม่มีรอยแตก รูพรุน หลุมอุกกาบาต และน้ำกระเซ็น และจะต้องไม่มีการตัดราคามุมภายในของแท่นทีจะต้องเป็นการเปลี่ยนแปลงที่ราบรื่นอุปกรณ์ท่อทั้งหมดต้องได้รับการตรวจสอบลักษณะพื้นผิว 100%รอยแตก มุมแหลม หลุม และข้อบกพร่องอื่น ๆ บนพื้นผิวของข้อต่อท่อจะต้องขัดด้วยเครื่องบด และการตรวจจับข้อบกพร่องของอนุภาคแม่เหล็กจะต้องดำเนินการที่สถานที่เจียรจนกว่าข้อบกพร่องจะถูกกำจัดความหนาของข้อต่อท่อหลังจากการขัดต้องไม่น้อยกว่าความหนาของการออกแบบขั้นต่ำ
6.5.การทดสอบต่อไปนี้จะต้องดำเนินการสำหรับอุปกรณ์ท่อที่มีข้อกำหนดพิเศษของลูกค้า:
6.5.1.การทดสอบอุทกสถิต
อุปกรณ์ท่อทั้งหมดสามารถผ่านการทดสอบไฮโดรสแตติกกับระบบได้ (แรงดันทดสอบไฮโดรสแตติกคือ 1.5 เท่าของแรงดันการออกแบบ และเวลาต้องไม่น้อยกว่า 10 นาที)ภายใต้เงื่อนไขว่าเอกสารใบรับรองคุณภาพเสร็จสมบูรณ์ อุปกรณ์ท่ออดีตโรงงานอาจไม่อยู่ภายใต้การทดสอบอุทกสถิต
6.5.2.ขนาดเกรนจริง
ขนาดเกรนจริงของข้อต่อท่อสำเร็จรูปต้องไม่หนากว่าเกรด 4 และความแตกต่างของระดับของข้อต่อท่อที่มีเลขความร้อนเท่ากันจะต้องไม่เกินเกรด 2 การตรวจสอบขนาดเกรนจะต้องดำเนินการตามวิธีการที่ระบุใน Yb / t5148-93 (หรือ ASTM E112) และเวลาตรวจสอบต้องเป็นครั้งเดียวสำหรับแต่ละหมายเลขความร้อน + แต่ละชุดการอบชุบด้วยความร้อน
6.5.3.โครงสร้างจุลภาค:
ผู้ผลิตจะต้องดำเนินการตรวจสอบโครงสร้างจุลภาคและจัดเตรียมภาพถ่ายโครงสร้างจุลภาคตามข้อกำหนดที่เกี่ยวข้องของ GB / t13298-91 (หรือมาตรฐานสากลที่เกี่ยวข้อง) และเวลาตรวจสอบจะต้องเป็นไปตามจำนวนความร้อน + ขนาด (เส้นผ่านศูนย์กลาง × ความหนาของผนัง) + ชุดการรักษาความร้อน ครั้งหนึ่ง.
7. บรรจุภัณฑ์และการระบุ
หลังจากแปรรูปอุปกรณ์ท่อแล้ว ผนังด้านนอกจะต้องเคลือบด้วยสีกันสนิม (สีรองพื้นอย่างน้อยหนึ่งชั้นและสีทาสำเร็จหนึ่งชั้น)สีทาผิวของชิ้นส่วนเหล็กกล้าคาร์บอนต้องเป็นสีเทา และสีทาผิวของชิ้นส่วนอัลลอยด์จะเป็นสีแดงสีจะต้องสม่ำเสมอไม่มีฟอง ริ้วรอย และลอกร่องจะต้องได้รับการปฏิบัติด้วยสารป้องกันสนิมพิเศษ
อุปกรณ์ท่อปลอมขนาดเล็กหรืออุปกรณ์ท่อที่สำคัญบรรจุในกล่องไม้และอุปกรณ์ท่อขนาดใหญ่มักจะเปลือยเปล่าหัวฉีดของข้อต่อท่อทั้งหมดจะต้องได้รับการปกป้องอย่างแน่นหนาด้วยวงแหวนยาง (พลาสติก) เพื่อป้องกันข้อต่อท่อจากความเสียหายตรวจสอบให้แน่ใจว่าสินค้าที่จัดส่งในขั้นสุดท้ายไม่มีข้อบกพร่องใดๆ เช่น รอยแตก รอยขีดข่วน รอยดึง ผิวสองชั้น การเกาะติดทราย การทับถม การรวมตัวของตะกรัน และอื่นๆ
ความดัน อุณหภูมิ วัสดุ เส้นผ่านศูนย์กลาง และข้อกำหนดอื่น ๆ ของข้อต่อท่อของข้อต่อท่อจะต้องทำเครื่องหมายที่ส่วนที่ชัดเจนของผลิตภัณฑ์ข้อต่อท่อซีลเหล็กใช้ซีลเหล็กความเค้นต่ำ
8. ส่งสินค้า
ต้องเลือกโหมดการขนส่งที่ผ่านการรับรองสำหรับการส่งมอบอุปกรณ์ท่อตามความต้องการของสถานการณ์จริงโดยทั่วไป อุปกรณ์ท่อในประเทศจะขนส่งโดยรถยนต์ในกระบวนการขนส่งรถยนต์ จำเป็นต้องมัดอุปกรณ์ท่อกับตัวรถให้แน่นด้วยเทปบรรจุภัณฑ์อ่อนที่มีความแข็งแรงสูงระหว่างการขับขี่ยานพาหนะ ไม่อนุญาตให้ชนและถูกับอุปกรณ์ท่ออื่นๆ และใช้มาตรการป้องกันฝนและความชื้น
HEBEI CANGRUN PIPELINE EQUIPMENT CO.,LTD เป็นผู้ผลิตอุปกรณ์ท่อ หน้าแปลน และวาล์วมืออาชีพบริษัทของเรามีทีมบริการด้านเทคนิคและวิศวกรรมที่มีประสบการณ์ด้านวิศวกรรมมากมาย เทคโนโลยีระดับมืออาชีพที่ยอดเยี่ยม การตระหนักรู้ในการบริการที่แข็งแกร่ง และการตอบสนองที่รวดเร็วและสะดวกสบายต่อผู้ใช้ทั่วโลกบริษัทของเราสัญญาว่าจะออกแบบ จัดระเบียบการจัดซื้อ การผลิต การตรวจสอบและทดสอบ บรรจุภัณฑ์ การขนส่ง และบริการตามข้อกำหนดของการจัดการคุณภาพ ISO9001 และระบบการประกันคุณภาพมีคำกล่าวโบราณในจีนว่า เป็นเรื่องน่ายินดีที่มีเพื่อนมาจากแดนไกล
ยินดีต้อนรับเพื่อน ๆ ของเราเข้าเยี่ยมชมโรงงาน
เวลาที่โพสต์: 06-06-2565